Case Study: hiTRAN® Installed into Feed/Effluent Exchangers
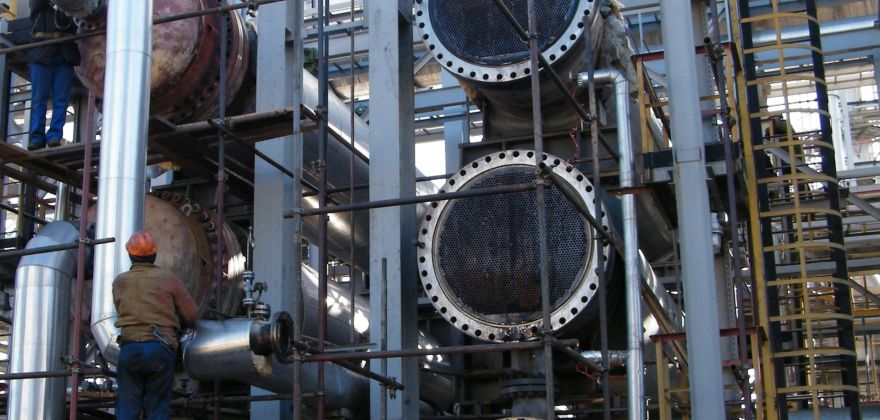
The Challenge
Since 1980, CALGAVIN’s primary technology hiTRAN® Thermal Systems, a tube side heat transfer enhancement product for industrial heat exchangers, has been used to optimise new designs for mainly utility heat exchangers, e.g. compressor lube oil air coolers, for many years. The hiTRAN product has also been retrofitted to key process heat exchangers giving the benefit of reduced capital costs removing the need to replace underperforming units. However, one pivotal retrofit case study does stand out amongst CALGAVIN’s catalogue that truly shows the power of heat transfer enhancement along with skilled analysis of a unit restricting a Refinery’s full capacity. For a long time, CALGAVIN has had representation for the CIS including Russia. During this time CALGAVIN has discussed many projects with End Users, one of which is Lukoil. The Lukoil Volgograd Refinery contacted us through our representatives, hi-Prom Bureau Ltd, and presented a high priority case to overcome. This already was a different project normally seen as it was in Russia, where traditionally it has been one of the harder territories for market accessibility and here was CALGAVIN being given the responsibility to provide a solution.
The design operation at Volgograd specified that Hydrotreatment proceeded in the catalyst of a reactor where crude feeding the whole Refinery was pumped from storage tanks and mixed with circulating Hydrogen. This feed entered feed/effluent heat exchangers where it was preheated on the shell side. The unit consisted of 6 shells in total, 2 in parallel and 3 in series, and the whole unit was designed at 120% performance.
However, the reality showed the feed to the unit and the fired heater were significantly lower in temperature. This, in turn, increased the load on the heater, resulting in higher than anticipated fuel/energy consumption when processing the full flow of the Refinery. In conclusion, this quantified to 21% less load on the feed/effluent exchangers which increased the duty of the fired heater downstream by 108%, significantly impacting the economics and energy efficiency of the plant. Our customer Lukoil saw this project as a high priority case as the Refineries’ operating costs needed to be reduced and plans for expansion were not feasible in the present circumstance.
The requirement set out by the customer was to optimise the performance of the feed/effluent heat exchangers. CALGAVIN would need to guarantee for 12 months the key target of preheating the feed stream to 313°C prior to the fired heater. Other corresponding parameters were to be met and any solution provided would have to be within the process pressure drop (~0.5bar for 3 shells).
The Solution
Prior to CALGAVIN’s involvement, the exchangers originally recovered 19 MW of heat from the effluent of a catalytic reactor. To bring the reactor feed up to its target temperature required a fired heater to add a further 4.1 MW. A proposed flowrate increase would have raised the exchanger duty to 28 MW and the fired heater duty to 6 MW. As well as being expensive in fuel, this would have been beyond the capacity of the fired heater as it was already operating at over 100% load.
CALGAVIN® engineers confirmed that tubeside heat transfer limited the exchanger’s performance, with poor tubeside bundle and flow distribution due to low pressure loss partly to blame. They designed hiTRAN Thermal Systems to increase tubeside heat transfer both directly, by increasing turbulence, and indirectly, by utilising more of the available tubeside pressure drop to improve fluid distribution. With careful analysis, the engineers tailored the geometry of hiTRAN to suit the changing proportions of liquid and vapour along with the exchanger. The simulation showed that at the higher flowrate, the hiTRAN Thermal System would increase the overall heat transfer coefficient by a factor of 2.6 (73>191 W/m2K), boosting heat recovery to 32.4 MW exceeding the required 28MW. With this much improved heat recovery, the fired heater duty downstream would reduce from 6.0 MW to only 2.0 MW.
After the retrofit of 15126 hiTRAN Thermal Systems in under 2 weeks, 2.2 MW, or 63 TJ/y, was immediately saved through increased heat recovery from the effluent stream at present conditions. LUKOIL valued the annual fuel saving at 7 million roubles (US$ 233,000). A test at the proposed higher flowrate confirmed that the hiTRAN Thermal Systems would have increased exchanger performance from 27.8 MW to 32.4 MW, saving 4.6 MW in total, without increasing the load on the fired heater. So not only did hiTRAN increase the efficiency of the exchangers by 16%, it avoided the high capital cost of commissioning a large new fired heater and potentially new feed/effluent units.
The Director General of Lukoil praised CALGAVIN saying ‘CALGAVIN Ltd completed the successful reconstruction of a hydrotreater as part of a catalytic reforming unit on the Volgograd Refinery. This retrofit with hiTRAN, enhanced the thermal rating and increased the duty of the heater while still reducing heat loss at the same time’.
This was a considerable step change in both our implementation of hiTRAN technology in other services but it truly proved that with good understanding and competency, novel technology like hiTRAN can benefit End User plants considerably whilst keeping within plant budgets and processing ‘greener’.