Optimise the Operational Efficiency of your Heat Exchanger
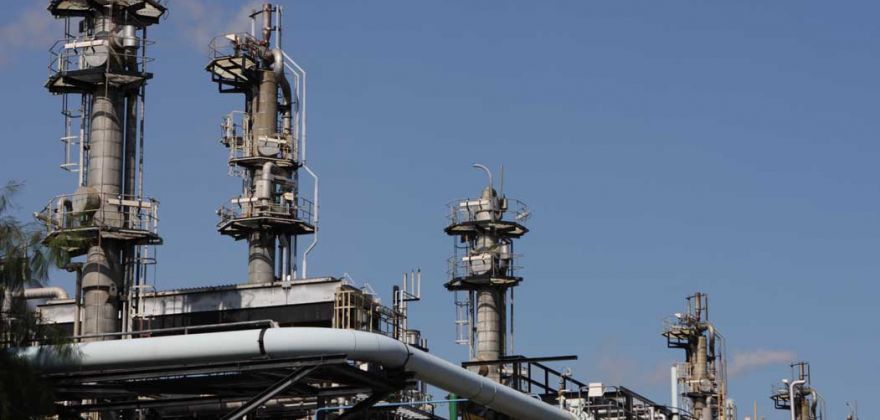
Heat exchangers are widely used in the chemical industry for processing and creating a number of industrial chemicals and related products. While heat exchangers are created in adherence to ASME codes after thorough research and planning in order to ensure design and process efficiency for optimal output, there are a number of operational factors that can affect its overall output.
We take a look at 8 simple measures you can implement to improve your heat exchanger’s efficiency and enjoy increased durability:
High Pressure Substances
Input high-pressure fluids on the tub side in order to minimize exchanger maintenance costs. This also helps in terms of performance efficiency as the smaller tube diameter has a higher pressure rating for the same metal thickness compared to that of a larger diameter shell.
Fouling
Fluids that have a higher tendency to foul should be put in from the tube side to allow the easy cleaning of the heat exchanger. This is done because cleaning straight tubes is usually easier than cleaning the sheet. However, this is largely subjective to the configuration of the heat exchanger. In case of fixed tubesheets, the clean fluid should be put on the sheet side, unless it is easy to clean the expected fouling with chemical solutions. In case of U-tubes, you can take a call on which side the fluid should be sent in depending on the presence of additional cleaning options like a fouling reduction setup since U-tubes are much tougher to clean as compared to straight tubes.
Corrosive Fluids
When working with corrosive fluids, you can simply put the corrosive fluids on the tube side. By using the tube side for corrosive liquids you can save costs as you will only need to make the tubes, tubesheets, heads and channels using expensive corrosion-resistant alloys. This turns out to be more cost-efficient as you would be required to make the entire exchanger out of corrosion-resistant alloys if you plan to use the shell side to protect it from deterioration.
Low-Pressure Drop
In the case of low-pressure drops, the fluid should go on the shell side due to the pressure drop sensitivity. In fact, an appropriate combination of baffle cut, spacing (segmental/double segmental) can accommodate nearly any pressure-drop requirement, so it is best to make that decision depending on the intended usage of the heat exchanger.
Vapor
Since vapor normally has a higher volume and a comparatively lower heat-transfer coefficient, it is best to allocate it to the shell side. This also reduces the pressure drop for a given volume while providing a higher heat-transfer coefficient.
Condensing Fluids
A condensing fluid most often goes on the shell side — but the choice demands careful evaluation. If the shell-side velocity is low enough, the vapor and liquid can separate inside the exchanger. The liquid dropping out makes the vapor leaner, reducing the temperature required to get more liquid to condense from the remaining vapor. For relatively pure mixtures, this effect is unimportant. For wide-condensing-range mixtures, ensure the overall flow pattern inside the exchanger keeps the liquid and vapor mixed. This may necessitate having the shell-side fluid leave from the bottom (forcing the liquid and vapor to mix) or determine the choice of baffling inside the exchanger (horizontal versus vertical or 45° baffle cut).
Viscous Substances
Since viscous fluids tend to have high pressure drop and low heat transfer on the tube side, shell-side allocation is more preferable. However, high pressure drops on the shell side are known to reduce the transfer of heat and the quality may also get affected due to vibration damage from a high pressure drop on the shell side. Therefore, it is best to make the necessary modifications in order to reduce such damage.
Solidifying Services
While it is advisable to avoid using shell and tube heat exchangers for any services that have a high risk of solidification and freezing, it is best to process such fluids on the tube side. The tube side is more preferable because in an instance where the fluid solidifies, you can simply pull out the tube bundle and replace it. On the other hand, if the solid is on the shell side, it will be impossible to remove the tube bundle, you will also be required to replace the entire exchanger.
Now, that you have a better idea of the probable outcome when it comes to processing different types of fluids and gases in a shell and tube heat exchanger, be sure to incorporate this knowledge when selecting the most appropriate heat exchanger to ensure operational longevity!
As this is a guest article the thoughts and opinions are of the author and not CALGAVIN®.